Nutze 5S zur Einführung von kontinuierlicher Verbesserung
In diesem Beitrag kannst Du mein Konzept zur Einführung von 5S nachvollziehen. Ich zeige Dir ganz offen mein Vorgehen, damit Du auch in Deinem Betrieb dauerhafte Ordnung einführen kannst. Weshalb das gleichzeitig einen Prozess der kontinuierlichen Verbesserung startet, erkläre ich Dir ganz am Ende.
„Mit 5S kann man die Mitarbeiter schon richtig vergraulen!“ … diese Aussage schon einmal gehört? Ich des Öfteren! Das kann auch auf jeden Fall zutreffen, denn falsch angegangen, wird 5S zu einer frustrierenden Erfahrung für alle Beteiligten. Damit Dir das nicht auch passiert, kannst Du Dir gerne einen Termin bei mir buchen.
Wird die 5S-Methode jedoch von Beginn an richtig eingeführt, entwickelt sie sich zu einer Maschine – eine Maschine für grundlegende Verbesserungen. 5S ermöglicht nicht nur die Steigerungen der Effizienz, der Arbeitssicherheit und der Mitarbeiterzufriedenheit, sondern unterstützt die gesamte Belegschaft beim Kulturwandel. Aus „Ich darf hier ja gar nichts entscheiden“ wird ein „Ich habe mal eben schnell diese Verbesserung umgesetzt“. Das macht richtig Spaß und bringt das ganze Unternehmen mit jeder Verbesserung einen Schritt zu mehr Erfolg – und Gewinn.
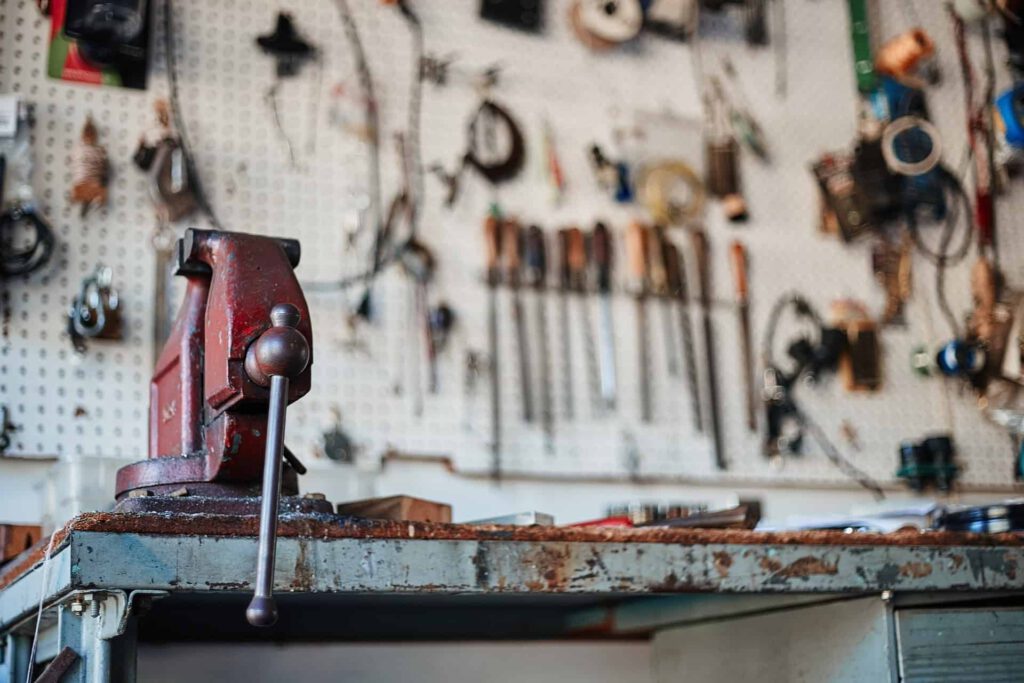
Warum 5S?
Ordnung, Sauberkeit und Arbeitssicherheit am Arbeitsplatz, so definiere ich immer 5S damit es jeder schnell und einfach verstehen kann. Natürlich steckt da deutlich mehr dahinter.
Das A und O bei der Anwendung von 5S ist der Bezug zur Wertschöpfung. 5S muss einen Unterschied in der täglichen Arbeit der Mitarbeiter ausmachen. Es muss darauf auswirken, wie schnell und wie gut ihr Kundenwünsche bedienen und Kundenprobleme lösen könnt. Der Kundennutzen muss absolut im Vordergrund stehen.
Wenn Du regelmäßig aufräumst und Dich wunderst, warum es nach kurzer Zeit wieder unordentlich ist, wirst Du das verstehen – reine Zeitverschwendung. Ziel ist es, dauerhaft für Ordnung zu sorgen und Verschwendungen, wie z. B. Laufen, Suchen, Warten, Umräumen, so gut es geht zu jeder Zeit zu minimieren. Für vollen Fokus auf die Wertschöpfung zum Kunden. Dabei hilft die 5S-Methode perfekt.
Was bedeutet 5S?
Natürlich stecken hinter den 5 „S“ ganz coole und bedeutende Begriffe. Trotzdem, die japanischen Abkürzungen (irgendwas mit Seiri…) und Hintergründe (natürlich aus Lean und von Toyota) erspare ich Dir. Über die einzelnen Schritte kannst Du überall sonst auch schon so viel lesen, deshalb hier keine Details.
Nur kurz die 5 Kernelemente auf Deutsch:
- Sortieren
- Systematisieren
- Säubern
- Standardisieren
- Selbstdisziplin üben und
ständig verbessern
So viel vorweg: die genannte und etablierte Reihenfolge gefällt mir bei der Einführung nicht 100%-ig. Niemand würde schließlich nach dem Sortieren, das schmutzige Werkzeug in das noch schmutzige Regal legen. Hier ist es definitiv sinnvoll, beides vorher zu reinigen (Schritt 3 also vor dem zweiten).
In der dauerhaften Anwendung müsst ihr die 5 Schritte jedoch gar nicht in eine Reihenfolge bringen. Sondern es ist viel wichtiger grundsätzlich alle 5S im Blick zu haben und regelmäßig zu überprüfen. Dabei steht das „dritte S – Säubern“ für dauerhafte Sauberkeit vor allem in Bezug auf das frühzeitige Erkennen von Problemen oder Schäden, während und durch das Reinigen.
Hervorzuheben ist das Zusammenspiel mit der Prozessbestätigung als wichtiger fünfter Bestandteil von 5S und Teil des Veränderungsmodells (Element Vorbildfunktion). Nach dem Motto: „Der Chef hat ein Auge drauf und fragt mich regelmäßig nach weiteren Verbesserungsideen.“ Also scheint es ihm wichtig zu sein, dann halte ich mich mal besser dran.
5S als Change Kick-Starter
Wichtiger als die genannten 5 Schritte auf Japanisch auswendig zu lernen, ist es die Philosophie zu verstehen. Ziel von 5S ist es ständig an den ersten 4 Schritten zu arbeiten und die Arbeitsplätze immer weiterzuentwickeln, zu verbessern und an neue Gegebenheiten anzupassen. Nach dem Motto: Ist das Optimum erreicht, setzen wir uns höhere Ziele! Deshalb ist 5S ein unschlagbarer Motor die Philosophie der kontinuierlichen Verbesserung in der Belegschaft zu verankern.
Damit daraus kein Rohrkrepierer wird, solltest Du bei der Auswahl des ersten 5S-Bereichs einiges beachten:
- Schaffe Mehrwert für den Betrieb
Welche erkannten Probleme sollen gelöst werden? Wo lässt sich die Durchlaufzeit dank kürzerer Wege oder weniger Suchen reduzieren? - Schaffe Mehrwert für die Mitarbeitenden
Welche erkannten Probleme sollen gelöst werden? Wo kann der Arbeitsplatz so gestaltet werden, dass die Belastung oder unnötige Bewegung der dort Tätigen minimiert wird? - Ermögliche häufige Anwendung
Der Pilotbereich sollte höchst frequentiert sein und das von unterschiedlichen Beschäftigten, damit möglichst viele in den Genuss der neuen Art zu arbeiten kommen und es möglichst schnell auf andere Bereiche ausweiten wollen.
Das möchte ich hier explizit noch einmal betonen. Die Auswahl des ersten 5S-Bereiches ist tatsächlich mit die wichtigste Entscheidung bei der 5S-Einführung. Liegt die daneben hat das nicht nur Auswirkung auf die aktuellen Bestrebungen 5S einzuführen, sondern die negative Erfahrung wird sich ins Gedächtnis der Mitarbeiter einbrennen. Dadurch wird jeder neue Anlauf für 5S umso schwerer. Melde Dich gerne, wenn Du auf Nummer sicher gehen möchtest.
Immer wichtig: Anforderungen der Arbeit und der Mitarbeiter einbeziehen
- Beziehe Mitarbeitende ein
Es bringt nichts, wenn die Auszubildenden (weil die haben ja eh Zeit) die tollsten 5S Bereiche erschaffen. Denn dann wird sich kein Geselle mit den Veränderungen identifizieren und folgerichtig diese nicht mit Leben füllen. Also gilt es die (führenden) Mitarbeitenden nicht nur bei der Auswahl des Bereiches einbeziehen, sondern von A bis Z – von Anfang bis Ende der Aktion. Für die Einführung und die Weiterentwicklung kann es von Vorteil sein, wenn Du Verantwortliche für einzelne Bereiche bestimmst. Das ist allerdings ein Thema für sich und Definitionssache (einzelne Verantwortliche vs. alle Nutzer sind verantwortlich, aber dazu vielleicht ein anderes Mal mehr). - Vermeide heilige Kühe
Um 5S nicht von vornherein zu verteufeln, solltest Du Dir über heilige Kühe bewusst werden und diese möglichst vermeiden. Personalisierte Werkzeugwagen gehören oft dazu. Auch wenn es dem Unternehmen einen Mehrwert bringen würde (weniger Werkzeug im Umlauf bei gleicher oder besserer Verfügbarkeit, standardisierte Aufbewahrung ohne Suchen und doppelte Wege, besserer Überblick über Anzahl und Qualität der Tools, maßgeschneiderte Werkzeugbehälter für häufige Tätigkeiten, Steigerung des Verantwortungsbewusstseins für die Sicherheit, Ordnung und Sauberkeit, …). Die damit verbundene Aufregung in der Belegschaft wäre definitiv hinderlich. Das heißt aber nicht, dass diese heiligen Kühe grundsätzlich tabu sind. In einer späteren Phase sollten diese ganz bewusst auch angegangen werden.
Der schwerste Part zum Schluss
- Begrenze den Umfang
Der Pilotbereich sollte so begrenzt wie möglich gewählt werden, damit die oben genannten Punkte Mehrwert und Frequenz noch gerade erfüllt sind. Niemand erkennt den Nutzen eines „Pilotbereiches“, wenn nach 2-3 Stunden 5S-Workshop noch die Hälfte fehlt und nur das erste oder zweite „S“ abgehakt sind. Vor allem, wenn sich das auch in den nächsten 4 Wochen nicht ändert. Zum Abschätzen des machbaren Umfanges ist einiges an Erfahrung nötig. Zu berücksichtigen sind u. a. die Anzahl der Gegenstände im Bereich, Verschmutzungsgrad, Anzahl der Teilnehmenden und die Vision für den Bereich (wie soll es mal aussehen?).
Hast Du schon Ideen für passende Bereiche? Melde Dich gerne bei mir und ich helfe Dir Deine Auswahl zu treffen.
Vorgehen zur Umsetzung
Jetzt wo Du den Pilotbereich festgelegt hast, solltest Du zwei Dinge tun. Eine Vision entwickeln (1) und den Punkt 5 („Selbstdisziplin üben und ständig verbessern“) vordenken (2).
(1) Entwickle, gerne zusammen mit etablierten Kollegen, eine Vision für diesen Bereich und auch schon eine grobe Idee von der weiteren Umsetzung im gesamten Betrieb. Wie soll der Bereich mal aussehen? Welche Arbeiten werden dort erledigt werden? Sind größere Umbauten erforderlich/geplant? Welche Methoden sollen für die Standardisierung verwendet werden (z.B. Fotos, Markierungen, Schaumstoff), damit alles bleibt wo es hingehört? Wie überträgt ihr 5S auf den gesamten Betrieb?
(2) Mach Dir vorab Gedanken über den Punkt 5 der 5S („Selbstdisziplin üben und ständig verbessern“), damit der erste Pilotbereich zum Erfolg und die Keimzelle für das gesamte Unternehmen wird. Dazu eignet sich am besten die Methode der Prozessbestätigung, die ihr dann nach und nach auch auf weitere Elemente ausweiten könnt (Standardarbeit, Problemlösung, Performance Management und alles Weitere, das neu eingeführt und einer Vorbildfunktion benötigt).
Wenn das steht, kannst Du den ersten 5S Pilot-Workshop als Auftakt für die „5S-isierung“ des ganzen Betriebes durchführen.
Auftakt als 5S Pilot-Workshop
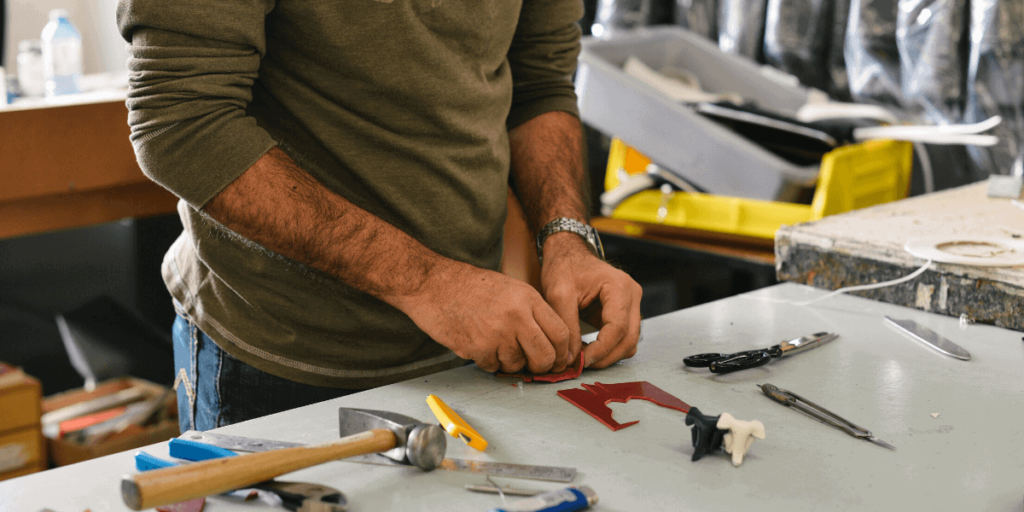
Nach meiner Erfahrung hat sich dieses Vorgehen für einen ersten 5S-Workshop bewährt:
- Start mit einer Einleitung mit Hintergründen:
Warum machen wir das (siehe oben)?
Wie gehen wir vor (Bereich eingrenzen, 5S Prinzipien anwenden)?
Was erwartest Du von den Mitarbeitenden (z. B. Mitarbeit, Ziel die ersten vier “S“) und was können sie von Dir erwarten (z. B. Unterstützung bei der Umsetzung ihrer Ideen)? - Zum Verdeutlichen der 5S-Prinzipien bieten sich ein Spiel an. Zum Beispiel dieses „5S – Zahlenspiel“, das Du hier downloaden kannst.
Danach geht’s los!
- Stelle Dir entlang der 5S, sprich (aus)sortieren, säubern, systematisieren und standardisieren, für jedes Teil in dem Bereich, diese vier grundlegenden Fragen:
- Wird das benötigt?
- Wie viel wird davon benötigt?
- Wo wird es benötigt?
- Was machen wir, damit es dort bleibt, wo es benötigt wird bzw. dahin zurückkommt?
- In drei beschrifteten Kisten (wird benötigt, Verwendung zu klären, Müll) können die Teile zwischen gelagert/sortiert werden. „Wird benötigt“ bleibt im Pilot-Bereich und wird im Laufe des Workshops wieder eingeräumt. „Verwendung zu klären“ wird zeitnah geklärt oder wandert nach 2-3 Wochen automatisch in die „Müll“-Kiste. „Müll“ sollte selbsterklärend sein. Zusätzlich, für sperrige Teile, die nicht in die Kisten passen oder sich nicht so leicht entfernen lassen, sollten Markierungen oder Beschriftungen mit der gleichen Logik vorhanden sein.
- Wie gesagt, fertigwerden ist das A und O! Dennoch sollte es für alles Weitere eine Maßnahmenliste mit Aufgabe, Zuständigkeit und Termin geben.
5S Vorbereitungsliste:
Aus diesem Vorgehen ergibt sich diese Vorbereitungsliste, die Du gerne nutzen kannst:
- Organisatorisches (Auswahl Teilnehmer, Einladung, Agenda, Einleitungstext, Spiel, Maßnahmenliste)
- Persönliche Schutzausrüstung (z. B. Staubmasken, Handschuhe)
- Reinigungsmaterial (z. B. Besen, Handfeger, Putzmittel, Mülltüten)
- Markierungsmaterial zur Standardisierung (siehe Vision). Dafür habe ich schon Wifi-Drucker und Laminiergerät im Workshop, sodass am Ende alle Teile mit einem Bild gekennzeichnet sind.
- Kisten mit den Beschriftungen und alternative Markierungen
Über Details könnten wir gerne in einem persönlichen Gespräch sprechen.
Warum gerade 5S als Keim des Kulturwandels?
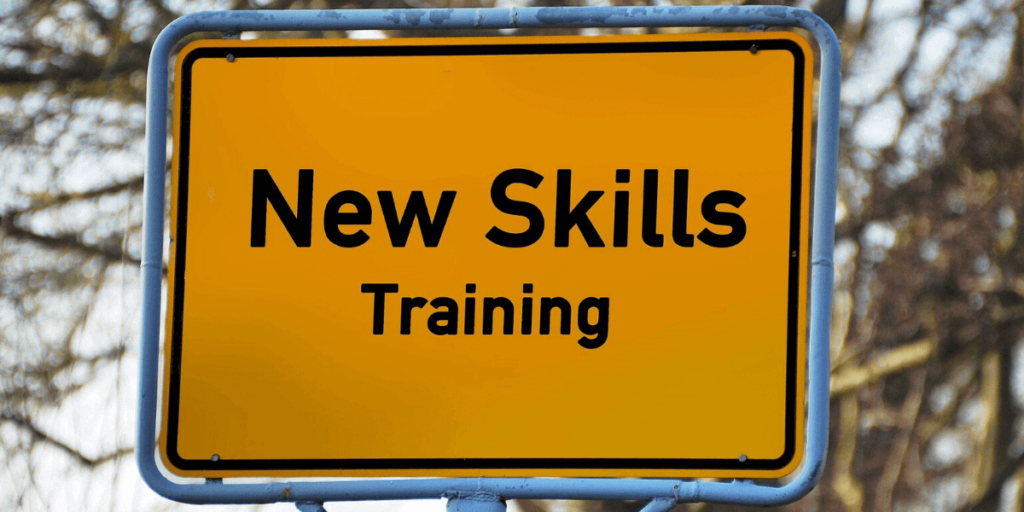
Kurz gesagt „Reach and Relevance“! 5S ist unschlagbar, weil Du damit die Möglichkeit hast die Mitarbeitenden direkt einzubeziehen und sofort einen Mehrwert für sie und das Unternehmen schaffen kannst. Außerdem können sie sehr schnell Verantwortung für Bereiche und die Weiterentwicklung übernehmen. Somit habe ich es schon mehrfach erlebt, dass sich 5S zu einem Selbstläufer entwickelt und die Mitarbeiter mit tollsten Ideen (sei es von Kundenbesuchen, durch Gespräche mit Bekannten oder auch von Pinterest!) immer neue Verbesserungen schaffen.
Wie sieht es in Deinem Betrieb aus? Ist die 5S-Methode für Dich relevant? Falls Du 5S in Deinem Unternehmen starten möchtest, lass uns gerne über das beste Vorgehen sprechen. Dafür kannst Du hier einen Termin vereinbaren.